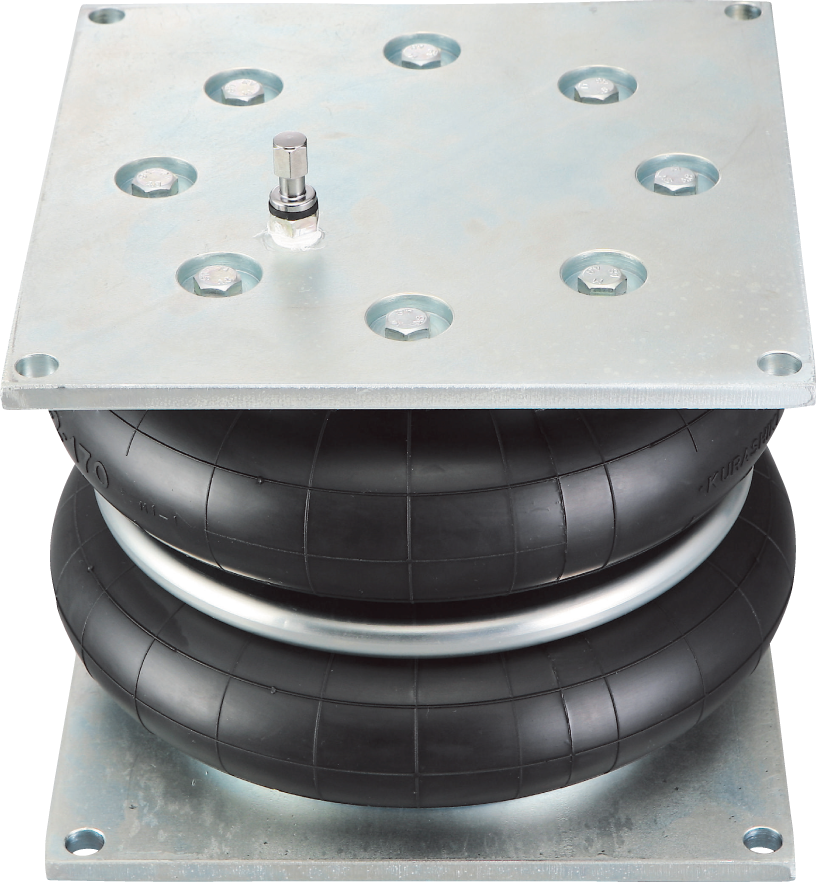
It has a low natural frequency and good anti-vibration effect.
A wide range of loads can be handled simply by changing the internal pressure, and the natural frequency (anti-vibration effect) is almost constant.
It does not have the surging phenomenon seen in coil springs, can isolate high-frequency vibrations, and has a soundproofing effect.
A softer spring constant can be obtained by using an auxiliary tank.
Air damping force can be used by providing a throttle at the connection between the auxiliary tank and the air spring.
A compact actuator with a low mounting height can be designed despite the large load and stroke.
Since there are no sliding parts, you can obtain an actuator that does not require lubrication or maintenance.
No. | Name | surface treatment | Features |
---|---|---|---|
① | Rubber bellows | Rubber bellows are made of synthetic rubber with excellent airtightness, high-strength reinforcing cords, It consists of a ringed steel wire (bead wire) at the end and has excellent durability. | |
② | Tightening ring | electrogalvanizing | The rubber bellows and mounting plate are secured by tightening the tightening bolts. Fix it airtight. |
③ | Intermediate ring | electrogalvanizing | Prevents rubber bellows from swelling due to air pressure. |
④ | On the mounting plate | electrogalvanizing | A metal fitting for mounting on a machine, with four mounting holes and an air vent. |
⑤ | Under mounting plate | electrogalvanizing | Mounting plate without air vents. |
⑥ | Tightening bolt | electrogalvanizing | - |
Number of steps | Part number | Standard height | Minimum height | Maximum height | Full stroke | Standard height | Bellows maximum outer diameter | Regular use maximum inner sho | Maximum use of Uchisho*1 | Allowable horizontal displacement | Allowable declination | ||
---|---|---|---|---|---|---|---|---|---|---|---|---|---|
Ho (mm) | Hmin (mm) | Hmax (mm) | X (mm) | Effective diameter D₀ (mm) | Effective pressure receiving area A₀ (cm2) | Internal volume Vₒ (cm3) | Dmax (mm) | P₀ (MPa) | Pmax (MPa) | (± mm) | (± degrees) | ||
1 | PSB-1-70 | 41 | 36 | 61 | 25 | 78 | 48 | 100 | 104 | 0.5 | 0.7 | 5 | 5 |
PSB-1-100 | 62 | 47 | 82 | 35 | 111 | 96 | 435 | 145 | 0.5 | 0.7 | 10 | 5 | |
PSB-1-130 | 102 | 50 | 132 | 82 | 142 | 158 | 2420 | 225 | 0.5 | 0.7 | 15 | 15 | |
PSB-1-145 | 102 | 50 | 132 | 82 | 158 | 196 | 2470 | 235 | 0.5 | 0.7 | 15 | 15 | |
PSB-1-170 | 102 | 50 | 132 | 82 | 182 | 260 | 3470 | 262 | 0.5 | 0.7 | 15 | 15 | |
PSB-1-230 | 102 | 50 | 137 | 87 | 245 | 470 | 5940 | 324 | 0.5 | 0.7 | 15 | 15 | |
PSB-1-300 | 102 | 50 | 137 | 87 | 309 | 750 | 9630 | 393 | 0.5 | 0.7 | 15 | 15 | |
PSB-1-360 | 102 | 50 | 137 | 87 | 369 | 1070 | 13660 | 457 | 0.5 | 0.7 | 15 | 15 | |
PSB-1-430 | 102 | 50 | 137 | 87 | 447 | 1570 | 19000 | 526 | 0.5 | 0.7 | 15 | 15 | |
PSB-1-500 | 102 | 50 | 137 | 87 | 508 | 2030 | 25200 | 594 | 0.5 | 0.7 | 15 | 15 | |
2 | PSB-2-110 | 117 | 73 | 151 | 78 | 111 | 97 | 1200 | 158 | 0.5 | 0.7 | 15 | 15 |
PSB-2-135 | 182 | 88 | 230 | 142 | 146 | 168 | 4110 | 222 | 0.5 | 0.7 | 15 | 15 | |
PSB-2-170 | 182 | 88 | 236 | 148 | 181 | 258 | 5470 | 262 | 0.5 | 0.7 | 20 | 15 | |
PSB-2-235A | 182 | 78 | 252 | 174 | 243 | 464 | 9630 | 321 | 0.5 | 0.7 | 20 | 15 | |
PSB-2-300A | 182 | 82 | 252 | 170 | 303 | 720 | 15400 | 389 | 0.5 | 0.7 | 20 | 15 | |
PSB-2-360A | 182 | 82 | 252 | 170 | 362 | 1030 | 19490 | 448 | 0.5 | 0.7 | 30 | 15 | |
PSB-2-430A | 182 | 86 | 272 | 186 | 438 | 1504 | 26340 | 522 | 0.5 | 0.7 | 30 | 15 | |
PSB-2-500A | 182 | 86 | 272 | 186 | 511 | 2050 | 35740 | 590 | 0.5 | 0.7 | 30 | 15 | |
3 | PSB-3-170 | 262 | 108 | 348 | 240 | 185 | 268 | 8350 | 254 | 0.5 | 0.7 | 20 | 10 |
PSB-3-235A | 262 | 108 | 362 | 254 | 240 | 452 | 14560 | 321 | 0.5 | 0.7 | 20 | 10 | |
PSB-3-360A | 262 | 108 | 390 | 282 | 366 | 1054 | 29080 | 443 | 0.5 | 0.7 | 20 | 10 |
*For the maximum internal pressure, please refer to the dimension/characteristics graph in the separate catalog.
1. Never inject air when the air spring is unloaded.
2. Be sure to remove the air before removing the air spring from the equipment or moving the equipment.
3. Be careful not to damage the rubber bellows of the air spring during installation and use.
Provide a protective cover if there is a risk of contact with foreign matter.
4. The ambient temperature for use should be -20°C to +60°C.
In environments exceeding 40°C, the life of air springs may be shortened.
5. Be careful not to let acids, alkalis, organic solvents, lubricating oils, etc. adhere to the rubber bellows.
In the unlikely event that it adheres, wash it with water immediately.
6. Use the air spring height within the range described in the catalog.
7. If the rubber bellows has a scratch reaching the reinforcing cord or an abnormal bulge, replace it immediately.
8. Make the installation surface of the air spring as flat as possible so that the entire plate surface receives the load.
Also, do not apply tension to the piping tube.
9. When using for anti-vibration purposes, keep the internal pressure below 0.5MPa.
When using for actuator applications, keep the internal pressure below 0.7 MPa. This 0.7MPa includes the instantaneous maximum internal pressure.
*For the usable range, please refer to the dimension/characteristics graph separately.
10.Use the 2-stage and 3-stage types only for actuator applications, and do not use them for vibration isolation.
Also, please do not hold for more than 10 minutes at the standard height or higher.
11.Do not weld the metal part of the air spring.
12.For anti-vibration purposes, do not use air springs for equipment that meets the following conditions.
①: When the operating speed (or operating stroke speed) of the device is close to the natural frequency of the air spring, 3 to 6 Hz.
This is the case, for example, for presses below 500 rpm.
②: For devices whose rotational speed rises and falls very slowly when starting and stopping, and whose resonance state continues for a long time.
③: Not applicable to (1), but the excitation force of the equipment is strong, and as a result, the amplitude of the air spring becomes excessive at the normal rotation speed.
Vibrating screens, vibrating conveyors, concrete block machines, concrete product manufacturing machines, commercial washing machines, centrifuges, compressors, vacuum pumps, high-speed presses
*In actual use (especially for items that have no track record of specifications), additional mass, dampers, stoppers, guides, etc. are used as necessary to achieve optimal matching that achieves both anti-vibration effects and vibration of equipment at a high level. , it is necessary to seek while doing trial and error.
Exposure equipment, electron microscope, three-dimensional measuring equipment, laser-related testing equipment, liquid crystal inspection equipment
Lifters, clamps, belt tension adjustment, roll pressure adjustment, ride-on game machines, roller coaster brakes
All rights reserved, © Copyright Kurashiki Kako Co., Ltd.
Feel free to contact us for a quote or inquiry